- 公開日:2021年09月09日
- | 更新日:2023年06月28日
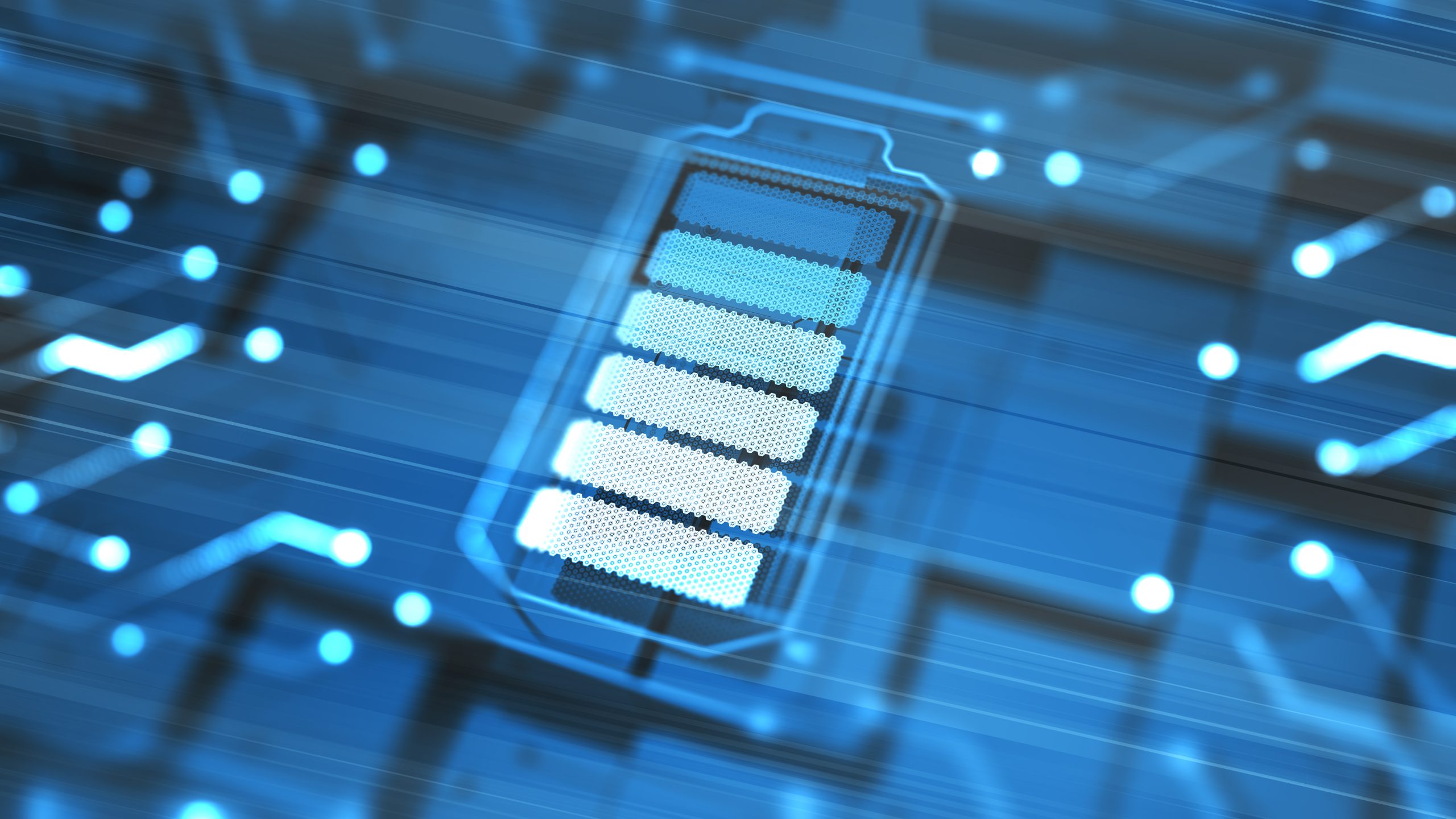
電池残量を検出する方法 第3話 Gas Gauge ICの設計フロー
- ライター:Yaita
- バッテリー管理IC
はじめに
Gas Gauge ICは電池残量の検出をおこなうデバイスの事です。
第1話では、Gas Gauge ICの役割とどのように残量検出をおこなっているかの基本概念を説明しました。
電池残量を検出する方法 第1話 Gas Gauge(電池残量計)とは
第2話では、Texas Instruments社(以降、TI社)のGas Gauge ICに使用されているアルゴリズム“CEDV”と”Impedance TrackTM”の概要を説明しました。
電池残量を検出する方法 第2話 Impedance TrackTMとは
本第3話では、TI社のこれらGas Gauge ICを題材に、基本的な設計フローについて説明したいと思います。
記事の末尾には、本記事で使用した設計ツールの操作方法をわかりやすく解説した資料もダウンロードいただけますので、是非最後までご覧ください。
TI社Gas Gauge ICの一般的な設計フロー
前記事で、TI社の残量検出アルゴリズムであるImpedance TrackTMとCEDVについて説明しました。アルゴリズムやデバイスによって設計フローは異なりますが、一般的な設計フローとしては以下手順になります。
1)Gas Gauge ICの選定
2)キャリブレーションの実施
3)TRM(Technical Reference Manual)を参照し、データメモリパラメータを設定
4)ラーニングサイクルの実施
5)ゴールデンファイルの抽出
6)実際の負荷にて常温、低温条件下での電池残量精度の確認
7)ゴールデンファイルを各ユニット(装置)にプログラム
8)シップモードにして出荷
本記事では、上記の一般的な設計フローに沿ってImpedance TrackTM、CEDVの設計フローを説明していきます。
Impedance TrackTMの設計フロー ~Flash Gauge~
まず予備知識として、Impedance TrackTMにはROM GaugeとFlash Gaugeの2種類があります。
ROM Gaugeは、電池のケミストリーに関連する情報(ChemID)が事前に書き込まれている製品ですが、使用可能な電池はdatasheet等に記載されたケミストリーに限定されます。
その一方で、Flash GaugeはChemIDをプログラムする必要がありますが、使用可能な電池は制限されておらず、カスタマイズ可能な製品です。製品ラインアップが多いのはFlash Gaugeの製品で、ROM Gaugeと比較すると残量検出精度が良い製品です。※ROM Gaugeの精度は~5%、Flash Gaugeの精度は~1%が目安です。
本記事では、製品ラインアップの多いFlash Gaugeの設計フローについて説明します。
1)Gas Gauge ICの選定
まずはGas Gauge ICの選定です。
電池のセルケミストリー(Li-ion/Li-Polymer等)や使用する電池の直列セル数から選定しますが、Gas Gauge ICにはシステムサイド用とパックサイド用があります。電池が取り外し可能であればシステムサイド用、電池とGas Gauge ICが常に接続されたアプリケーションであればパックサイド用のGas Gauge ICを使用します。
2)キャリブレーションの実施
図1の構成でbqStudioを使用しキャリブレーション(電圧、電流、温度、CC Offset、Board Offset)を実施します。
※bqStudioは本記事最後に紹介しているTI社が用意している設計ツールです。
図1 キャリブレーション実施時の構成
3)TRM(Technical Reference Manual)を参照し、データメモリパラメータを設定
3-1)ChemIDの特定
Impedance TrackTMの場合、まず電池のChemIDを特定する必要があります。
使用する電池が既存のChemIDリストに既に登録されていればそのままGas Gauge ICにプログラムすれば良いのですが、ChemIDリストに登録が無い場合は、オンラインツールGPCCHEMを用いて、使用する電池に近いChemIDを選択する必要があります。bqStudioで電圧、電流、温度のログを取りながら放電試験をおこない、GPCCHEMツールで結果をアップロードすると、電池にマッチするChemIDがフィードバックされますので、そのChemIDをプログラムします。
-GPCCHEM:
https://www.tij.co.jp/tool/jp/GPCCHEM
図2 GPCCHEMでの放電試験ログ
3-2)データフラッシュパラメーターの設定
次に、データフラッシュパラメーターを設定します。設定すべき最低限のパラメーターを以下に記載しています。
※詳細は使用するデバイスのTRM(Technical Reference Manual)をご参照ください。
- Design Capacity:電池の公称容量
- Design Voltage:電池の公称電圧
- Taper Current:C/10~C/20で設定
- Charge(Chg), Discharge(Dsg) current threshold:Taper Currentより小さな値で設定
- Quit current:Charge(Chg), Discharge(Dsg) current thresholdより小さな値、かつC/20以下の値で設定
- Terminate voltage:電池が放電可能な最低電圧(SOCが0%となる電池電圧)
- Charging Voltage:電池の満充電電圧(SOCが100%となる電池電圧)
4)ラーニングサイクルの実施
ChemIDとデータフラッシュパラメーターをプログラム後、ラーニングサイクルをおこないます。
ラーニングサイクルは実際の電池の内部抵抗情報(Raテーブル)と電池本来の容量であるQmaxを学習するためのプロセスです。
※詳細は使用するデバイスのTRM(Technical Reference Manual)をご参照ください。
- IT enableコマンド(0x21)を発行後、resetコマンド(0x41)を発行
- C/5~C/7の定電流負荷でterminate voltage(終端電圧)まで放電
- 5時間以上のリラックスタイム
- 満充電になるまで(設定したTaper current以下になるまで)充電
- 2時間以上のリラックスタイム後、Update Statusが以下になっていることを確認 ※Qmaxはこのタイミングで更新
システムサイド用Gas Gauge ICの場合:Update Statusが00→01
パックサイド用Gas Gauge ICの場合:Update Statusが04→05 - C/5~C/7での定電流負荷でterminate voltage(終端電圧)まで放電 ※Raテーブルはこのタイミングで更新
- 5時間以上のリラックスタイム後、Update Statusが以下になっていることを確認
システムサイド用Gas Gauge ICの場合:Update Statusが01→02
パックサイド用Gas Gauge ICの場合:Update Statusが05→06
図3 ラーニングサイクル
ラーニングサイクルについて資料を用意しています。以下からダウンロードすることができますので、ぜひご活用ください。
5)ゴールデンファイルの抽出
次に、bqStudioでゴールデンファイルを抽出します。それぞれのフォーマット
・srec:標準のモトローラフォーマットファイル
・bqfs:インストラクションフラッシュ+データフラッシュを含んだフラシュストリームファイル
・dffs:データフラッシュのみを含んだフラシュストリームファイル
6)実際の負荷にて常温、低温条件下での電池残量精度の確認
満充電からterminate voltage(終端電圧)になるまで放電させ、ログ結果からクーロンカウンタの計算によって真のFCCを算出し、「真のFCCからクーロンカウンタで積算された容量を差し引いた残容量÷真のFCC」を計算してSOCを計算し、Gas Gauge ICから読みだしたSOCと比較します。
7)ゴールデンファイルを各ユニット(装置)にプログラム
抽出したゴールデンファイルを各ユニットにプログラムします。
キャリブレーション値に関しては、一般的には、10台の基板で平均化したキャリブレーション値をゴールデンファイルに書き込みますが、特に高精度な残量検出が求められるアプリケーションでは、各ユニットのキャリブレーション値をそれぞれの基板に書き込みます。
8)シップモードにして出荷
IT enableコマンド(0x21)を発行し、デバイスをシップモード(低電力モード)にして出荷します。
CEDVの設計フロー
次にCEDVの設計フローを説明します。
1)~8)までの手順でImpedance TrackTMと異なるのは3)と4)のみですので、異なる部分のみ記載します。
3)TRM(Technical Reference Manual)を参照し、データメモリーパラメータを設定
データフラッシュパラメーターを設定します。設定すべき最低限のパラメーターを以下に記載しています。
※詳細は使用するデバイスのTRM(Technical Reference Manual)をご参照ください。
- EDV2, EDV1, EDV0:それぞれ7%, 3%, 0% SOCに設定 ※CEDV特有のパラメータ設定
- Design Capacity:電池の公称容量
- Design Voltage:電池の公称電圧
- Taper Current:C/10~C/20で設定
- Chg current threshold:Taper Currentより小さな値で設定
- Quit current:Taper Currentより小さな値でC/20以下の値で設定
- Terminate voltage:電池が放電可能な最低電圧(SOCが0%となる電池電圧)
- Charging voltage:満充電電圧を設定
4)ラーニングサイクルの実施
CEDVでは、前記事”Impedance TrackTMとは?”で説明した、電池のモデリングを以下ツールにて行います。
-GPCCEDV:
https://www.tij.co.jp/tool/jp/GPCCEDV
実際に使用する電池を用いて、3つの温度条件下(5℃, 30℃, 50℃)、2つの異なる放電レート(使用アプリケーションにおける平均のtyp, max電流値)で満充電から完全放電までの計6つのデータを取得することで、その電池のプロファイルに一致する7つのCEDVパラメータ(EMF, C0, R0, T0, R1, TC, C1)が提供されますのでこれらをGas Gauge ICにプログラムします。
※これは、言わばImpedance TrackTMのChemIDの特定に代わる作業で、厳密にいうとCEDVではラーニングサイクルのような手順は必要ありません。
設計ツール bqStudioの紹介
本記事で何度か登場したbqStudioはTI社が用意している設計ツールです。TI社の主要なGas Gauge ICは本ツールを使用して設計(コンフィグレーション)と評価を実施することができ、本記事でも説明している、キャリブレーションやラーニングサイクルの実行、ゴールデンファイルの生成等が可能です。
-BQSTUDIO:
https://www.tij.co.jp/tool/jp/BQSTUDIO
弊社ではbqStudioの操作方法をまとめた資料を用意しています。以下からダウンロードすることができますので、ぜひご活用ください。
まとめ
本記事ではImpedance TrackTM (Flash Gauge)とCEDVアルゴリズムを持つGas Gauge ICの一般的な設計フローを説明させていただきました。
Gas Gauge ICは汎用的なデバイスと比較して特有の設計フローになりますので、初めてTI社のGas Gauge ICを設計される方は、まずは本記事を参照頂いて設計の流れを把握して頂くとスムーズに開発いただけるかと思います。
本記事がご開発時のお役立ちになれば幸いです。
・参考リンク:
-Fundamentals of battery gauging algorism:
https://training.ti.com/fundamentals-battery-gauging-algorithm
-Start Guide for BQ Products:
https://www.tij.co.jp/jp/lit/an/sluaa98/sluaa98.pdf